- Acronym Guide
- AAM
- ABS
- AC
- ACAS
- ADS-B
- AFAC
- AGL
- AI
- AIM
- ALS
- AM
- AMA
- ANSP
- AOI
- APPI
- AUV
- AUVSI
- ARPAS-UK
- ASTM
- ATC
- BVLOS
- CAA
- CAAC
- CAB
- CASA
- CATT
- CBO
- CBR
- CBRN
- CDMA
- CDR
- CFR
- CIR
- COA
- COMINT
- CORS
- COTP
- COTR
- CPTED
- CV
- C2
- DAA
- DEM
- DFI
- DFS
- DGCA
- DHS
- DOD
- DPA
- DPEs
- DRG
- DRO
- DSM
- DSMX
- DSP
- DSSS
- DTM
- EASA
- EFT
- EO
- EOD
- EO/IR
- ELINT
- EMI
- ESC
- EVLOS
- eVTOLs
- FAA
- FCC
- FCS
- FHSS
- FICCI
- FLIR
- FOB
- FOV
- FPS
- FPV
- GBDAA
- GCP
- GCS
- GDPR
- GML
- GNSS
- GPS
- GSD
- GVC
- HDR
- HOGE
- IACRA
- ICAO
- ICS
- IMU
- INS
- IR
- ISA
- ISR
- ITU
- JARUS
- LAAMS
- LAANC
- LAATM
- LAI
- LBA
- LIDAR
- LOS
- LSALT
- MAC
- MAVLink
- MLIT
- MMS
- MSL
- MTOM
- NDAA
- NCSL
- NFZ
- NIST
- NMEA
- NOTAM
- NPA
- NPRM
- NTIA
- OBIA
- OEM
- OFDM
- OOP
- PASM
- PAV
- PCV
- PdM
- PEC
- PIC
- PID
- PIPL
- PLD
- PM
- PN
- PPK
- PPS
- PSM
- PWM
- UAM
- UAOP
- UAS
- UASTM
- UAV
- UCAVs
- UHD
- UHF
- USV
- UTM
- RAIM
- RCC
- RCS
- RFI
- ReOC
- RePL
- RMS
- ROI
- RPAS
- RPC
- RTH
- RTK
- SaR
- SAR
- SARP
- SBAS
- S.Bus
- SBIR
- SEDENA
- SfM
- SFOC
- SIGINT
- SLAM
- SMS
- SORA
- STANAG
- STTR
- sUAS
- TCAS
- TCCA
- TFR
- TIN
- TOF
- TP
- TPS
- TSA
- VHF
- VLOS
- VTOL
Drone Acronyms
What is PWM (Pulse Width Modulation)?
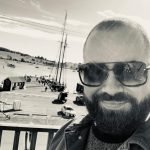
By
Jacob StonerTable Of Contents

Definition
PWM stands for Pulse Width Modulation, a technique used to control the amount of power delivered to an electrical device by modulating the width of the pulses in a signal. In PWM, the signal switches between on and off states at a consistent frequency, and the duration of the “on” phase within each cycle, known as the duty cycle, determines the average power supplied. PWM is widely used for controlling motors, lights, and other electronic components, including those in drones.
Usage
In drones, PWM is commonly used to regulate the speed of the motors by varying the power delivered to the electronic speed controllers (ESCs). By adjusting the duty cycle, the drone can control motor speed, enabling precise maneuvers and altitude adjustments. Additionally, PWM signals are used to transmit control commands from the receiver to various components like servos and ESCs, allowing for fine-grained control of flight dynamics.
Relevance to the Industry
Pulse Width Modulation is essential in drone technology due to its efficiency, simplicity, and accuracy. It provides smooth control over motor speeds and other actuator positions without generating excessive heat or energy loss. As a result, PWM contributes to better energy management and longer flight times, which are critical for both recreational and commercial drone applications. Its role in transmitting control signals also makes it a fundamental aspect of drone communication systems.
How Does Pulse Width Modulation (PWM) Work?
Generating and Modulating the Signal:
- Fixed Frequency and Duty Cycle:
- On-Off Pulses: Pulse Width Modulation generates a series of on-off pulses at a fixed frequency, switching between the high (on) and low (off) states. The duration of the “on” time within each pulse cycle, known as the duty cycle, controls the average power delivered. For example, a duty cycle of 50% means the signal is on for half of each cycle, delivering half the maximum power.
- Adjusting Duty Cycle to Control Power: By varying the duty cycle, PWM modulates the amount of power reaching a device without changing the frequency. A higher duty cycle increases the average power, resulting in greater output (e.g., motor speed), while a lower duty cycle decreases the average power.
- Controlling Motor Speed and Power Delivery:
- Speed Regulation in Drones: In drone applications, PWM signals sent to the electronic speed controllers (ESCs) regulate motor speed. The ESCs interpret the duty cycle to determine how much power to supply to the motors. A higher duty cycle translates to more power, increasing motor speed, while a lower duty cycle reduces speed. This allows for precise control over each motor, enabling stable and responsive flight.
- Efficient Power Delivery: PWM provides power in short bursts, which minimizes energy loss as heat and makes it highly efficient. Since the signal is either fully on or off, the power transistors in the ESCs spend less time in intermediate states, which reduces heat generation and improves the overall energy efficiency of the drone.
Transmitting Control Signals in Drone Systems:
- Sending Control Signals to Components:
- Flight Controller to ESCs and Servos: The flight controller sends PWM signals to various components like ESCs for motor control and servos for adjusting control surfaces or camera gimbals. Each signal consists of a pulse with a width corresponding to the desired position or speed. For instance, in a typical RC system, a pulse width of 1,000 to 2,000 microseconds is used to control the angle of a servo or the speed of an ESC.
- Standardization and Compatibility: PWM signals are widely used in radio-controlled systems due to their compatibility with a variety of servos and ESCs. This standardization ensures that different components can communicate effectively, making it easier to integrate and replace parts.
- Multiple Channels and Simultaneous Control:
- Dedicated Channels for Each Component: In a typical drone, each motor or servo is connected to a separate channel on the flight controller, allowing individual PWM signals to be sent to each component. This enables simultaneous control of multiple motors or servos, which is essential for coordinated maneuvers and stable flight.
- Sequential Transmission: PWM channels operate in sequence, with each signal pulse lasting a few milliseconds. The flight controller continuously cycles through the channels, updating the duty cycle for each component based on the latest control inputs. This rapid cycling allows for real-time adjustments and smooth control.
Applications and Advantages of PWM:
- Efficient Speed and Position Control:
- Direct Control Over Motor Speed: PWM’s ability to regulate power through duty cycle adjustment allows precise motor speed control, which is crucial for maintaining altitude, stability, and responsiveness in drones. This is especially important for applications like racing drones, where quick and accurate speed changes are essential.
- Smooth Positioning for Servos: PWM provides a smooth and precise way to control servo positions, making it ideal for applications like camera gimbals. Adjusting the pulse width changes the angle of the servo arm, allowing for accurate camera movements or control surface adjustments in fixed-wing drones.
- Advantages of Using PWM:
- Reduced Power Loss: PWM minimizes power loss by switching fully on or off, rather than partially, which reduces heat generation and improves battery efficiency. This advantage extends flight times and enhances the durability of drone components.
- Low Complexity and High Compatibility: PWM signals are relatively simple to generate and interpret, making them compatible with a wide range of RC components and accessible for hobbyists and professionals alike.
Interfacing with Other Modulation Techniques:
- Integration with Digital Control Systems:
- Signal Conversion for Advanced Control: In digital systems, PWM signals can be converted into other forms of modulation, like Pulse Code Modulation (PCM), to interface with advanced control systems. This allows for enhanced functionality, such as digital feedback loops or automated control adjustments.
- Use in Hybrid Systems: PWM is often combined with other modulation techniques, such as S.Bus or DSMX, for enhanced communication capabilities in drones. While PWM handles basic motor and servo control, other protocols manage complex data, telemetry, or remote settings.
- Applications Beyond Drone Control:
- LED Brightness and Power Control: PWM is also used to control LED brightness and power delivery in other electronics, demonstrating its versatility across various fields. In drones, PWM can control auxiliary components like LED indicators, enhancing both functionality and aesthetics.
By modulating the width of each pulse, Pulse Width Modulation (PWM) offers efficient and precise control over motor speed, servo positioning, and power delivery, making it a foundational technology in drone systems and a variety of electronic applications.
Example in Use
“The drone’s electronic speed controllers (ESCs) receive PWM signals from the flight controller to adjust the speed of each motor, enabling stable flight and responsive control.”
Frequently Asked Questions about PWM (Pulse Width Modulation)
1. How does PWM control motor speed?
Answer: PWM controls motor speed by adjusting:
- Duty Cycle: The proportion of time the signal is “on” during each cycle. A higher duty cycle results in more power to the motor, increasing its speed.
- Frequency Consistency: The signal switches on and off at a consistent frequency, allowing for precise control over power delivery without changing the signal’s frequency.
2. What are the advantages of PWM?
Answer: PWM offers several advantages:
- Energy Efficiency: By switching between full on and off states, PWM minimizes energy loss as heat, improving overall efficiency.
- Precision Control: It allows for smooth and precise control over devices like motors, which is critical for applications that require accurate adjustments, such as drone flight.
3. How is PWM used in drone communication?
Answer: PWM is used in drone communication by:
- Transmitting Control Signals: The flight controller sends PWM signals to ESCs and servos to control motor speeds, gimbal angles, and other components.
- Compatibility with RC Systems: Many radio-controlled systems use PWM to transmit signals from the receiver to the flight controller, simplifying communication and enabling responsive flight control.
For examples of these acronyms visit our Industries page.
As the CEO of Flyeye.io, Jacob Stoner spearheads the company's operations with his extensive expertise in the drone industry. He is a licensed commercial drone operator in Canada, where he frequently conducts drone inspections. Jacob is a highly respected figure within his local drone community, where he indulges his passion for videography during his leisure time. Above all, Jacob's keen interest lies in the potential societal impact of drone technology advancements.