- Acronym Guide
- AAM
- ABS
- AC
- ACAS
- ADS-B
- AFAC
- AGL
- AI
- AIM
- ALS
- AM
- AMA
- ANSP
- AOI
- APPI
- AUV
- AUVSI
- ARPAS-UK
- ASTM
- ATC
- BVLOS
- CAA
- CAAC
- CAB
- CASA
- CATT
- CBO
- CBR
- CBRN
- CDMA
- CDR
- CFR
- CIR
- COA
- COMINT
- CORS
- COTP
- COTR
- CPTED
- CV
- C2
- DAA
- DEM
- DFI
- DFS
- DGCA
- DHS
- DOD
- DPA
- DPEs
- DRG
- DRO
- DSM
- DSMX
- DSP
- DSSS
- DTM
- EASA
- EFT
- EO
- EOD
- EO/IR
- ELINT
- EMI
- ESC
- EVLOS
- eVTOLs
- FAA
- FCC
- FCS
- FHSS
- FICCI
- FLIR
- FOB
- FOV
- FPS
- FPV
- GBDAA
- GCP
- GCS
- GDPR
- GML
- GNSS
- GPS
- GSD
- GVC
- HDR
- HOGE
- IACRA
- ICAO
- ICS
- IMU
- INS
- IR
- ISA
- ISR
- ITU
- JARUS
- LAAMS
- LAANC
- LAATM
- LAI
- LBA
- LIDAR
- LOS
- LSALT
- MAC
- MAVLink
- MLIT
- MMS
- MSL
- MTOM
- NDAA
- NCSL
- NFZ
- NIST
- NMEA
- NOTAM
- NPA
- NPRM
- NTIA
- OBIA
- OEM
- OFDM
- OOP
- PASM
- PAV
- PCV
- PdM
- PEC
- PIC
- PID
- PIPL
- PLD
- PM
- PN
- PPK
- PPS
- PSM
- PWM
- UAM
- UAOP
- UAS
- UASTM
- UAV
- UCAVs
- UHD
- UHF
- USV
- UTM
- RAIM
- RCC
- RCS
- RFI
- ReOC
- RePL
- RMS
- ROI
- RPAS
- RPC
- RTH
- RTK
- SaR
- SAR
- SARP
- SBAS
- S.Bus
- SBIR
- SEDENA
- SfM
- SFOC
- SIGINT
- SLAM
- SMS
- SORA
- STANAG
- STTR
- sUAS
- TCAS
- TCCA
- TFR
- TIN
- TOF
- TP
- TPS
- TSA
- VHF
- VLOS
- VTOL
Drone Acronyms
What is ABS (Acrylonitrile Butadiene Styrene)?
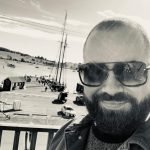
By
Jacob StonerTable Of Contents

ABS Definition
ABS (Acrylonitrile Butadiene Styrene) is a lightweight, durable, and impact-resistant thermoplastic commonly used in drone manufacturing. Known for its strength and flexibility, Acrylonitrile Butadiene Styrene is a popular material for drone frames, propellers, and other structural components. Its ability to absorb shocks and withstand harsh environmental conditions makes it ideal for both recreational and professional drone applications.
ABS Usage
In drones, Acrylonitrile Butadiene Styrene is often used to construct lightweight and resilient components, such as propeller guards, housings, and external frames. Its moldability allows manufacturers to create complex shapes and designs, ensuring both functionality and aesthetics. Additionally, Acrylonitrile Butadiene Styrene is cost-effective, making it a preferred choice for consumer-grade drones.
ABS Relevance to the Industry
Acrylonitrile Butadiene Styrene contributes to the durability and affordability of drones, particularly for entry-level models and hobbyist builds. Its resilience ensures that drones can endure minor crashes and impacts, while its lightweight properties enhance flight efficiency and battery life. As drone technology advances, Acrylonitrile Butadiene Styrene remains a key material for balancing cost, durability, and performance.
How Does Acrylonitrile Butadiene Styrene (ABS) Work in Drones?
Material Composition and Properties:
- What is Acrylonitrile Butadiene Styrene?
- Polymer Composition: ABS is a thermoplastic polymer made from three monomers:
- Acrylonitrile: Provides chemical resistance and hardness.
- Butadiene: Contributes impact resistance and flexibility.
- Styrene: Adds strength and a smooth, glossy finish.
- Key Characteristics: ABS combines these properties to create a material that is lightweight, durable, impact-resistant, and easy to mold.
- Polymer Composition: ABS is a thermoplastic polymer made from three monomers:
- Behavior Under Stress:
- Impact Resistance: Acrylonitrile Butadiene Styrene can absorb shocks and resist cracking under minor impacts, making it ideal for drone frames and protective parts.
- Flexibility: The material has enough elasticity to bend slightly under stress, reducing the risk of permanent damage.
- Temperature Sensitivity: Acrylonitrile Butadiene Styrene softens under high heat but performs well in most operational temperatures for drones.
Applications in Drone Manufacturing:
- Structural Components:
- Drone Frames: Acrylonitrile Butadiene Styrene is often used for drone bodies and frames due to its balance of strength, weight, and flexibility. It can endure minor crashes and impacts without shattering.
- Propeller Guards: Acrylonitrile Butadiene Styrene is molded into propeller guards to protect the drone’s blades and surrounding objects during operation.
- Housings and Covers: The smooth finish of Acrylonitrile Butadiene Styrene makes it suitable for camera housings, battery covers, and other external parts.
- Custom Designs:
- Moldability: ABS’s thermoplastic nature allows manufacturers to mold it into complex shapes, enabling innovative drone designs that optimize aerodynamics and aesthetics.
- Color and Texture Options: Acrylonitrile Butadiene Styrene can be colored or textured, enhancing the visual appeal and branding of consumer drones.
Advantages in Drone Operations:
- Lightweight and Durable:
- Enhanced Flight Efficiency: The lightweight nature of Acrylonitrile Butadiene Styrene reduces the overall weight of drones, improving flight time and maneuverability.
- Crash Resilience: Acrylonitrile Butadiene Styrene components absorb impact energy, protecting internal systems like flight controllers, cameras, and batteries.
- Cost-Effectiveness:
- Affordable Production: Acrylonitrile Butadiene Styrene is less expensive than materials like carbon fiber or aluminum, making it ideal for budget-friendly drones.
- Scalability: Its low cost and ease of manufacturing allow for mass production, reducing consumer prices.
Limitations and Challenges:
- Heat Sensitivity:
- Deformation Risks: Acrylonitrile Butadiene Styrene can warp or deform when exposed to high temperatures, such as prolonged sunlight or overheating motors.
- Operational Limits: While suitable for most consumer drones, ABS may not withstand extreme conditions faced by industrial or high-performance UAVs.
- Strength Limitations:
- Load-Bearing Capacity: Acrylonitrile Butadiene Styrene is less rigid than materials like carbon fiber, limiting its use in drones requiring high structural integrity or heavy payloads.
- Wear and Tear: Over time, Acrylonitrile Butadiene Styrene components may show signs of wear, such as surface scratches or minor cracks.
Maintenance and Longevity:
- Durability Over Time:
- Regular Inspections: Operators should check ABS components for cracks or deformations, especially after crashes or heavy use.
- Repair and Replacement: Damaged ABS parts can often be replaced easily due to their low cost and wide availability.
- Compatibility with Repairs:
- Adhesive Bonding: ABS parts can be repaired using specialized adhesives or epoxy, ensuring quick fixes for minor damage.
- 3D Printing: ABS is a popular material for 3D printing, enabling drone enthusiasts to create or replace custom parts on demand.
Integration with Advanced Materials:
- Hybrid Designs:
- ABS with Reinforcements: Some manufacturers combine ABS with other materials, such as carbon fiber reinforcements, to improve strength without significantly increasing weight or cost.
- Blended Components: ABS may be used alongside stronger materials for non-structural parts, optimizing cost and performance.
- Recyclability and Sustainability:
- Recycling Potential: ABS is recyclable, making it a more sustainable option compared to some thermosetting plastics.
- Environmental Considerations: Manufacturers are exploring eco-friendly ABS variants to reduce environmental impact.
By leveraging its lightweight, durable, and cost-effective properties, Acrylonitrile Butadiene Styrene (ABS) serves as a foundational material in drone manufacturing, enabling the production of resilient and affordable drones for hobbyists and professionals alike.
Example in Use
“The drone’s ABS frame absorbed the impact during a minor crash, protecting the internal components and allowing the flight to continue.”
Frequently Asked Questions about ABS (Acrylonitrile Butadiene Styrene)
1. Why is ABS used in drone manufacturing?
Answer: ABS is used because:
- It is lightweight, reducing the overall weight of the drone.
- It is impact-resistant, absorbing shocks and protecting internal components.
- It is cost-effective and easy to mold into complex shapes.
2. How does ABS compare to other materials like carbon fiber?
Answer:
- Durability: ABS is less durable than carbon fiber but sufficient for hobby-grade drones.
- Cost: ABS is more affordable, making it ideal for consumer drones.
- Weight: While ABS is lightweight, carbon fiber offers superior strength-to-weight ratio.
3. What are the limitations of ABS in drones?
Answer:
- Heat Sensitivity: Acrylonitrile Butadiene Styrene can deform under high temperatures.
- Limited Strength: It may not provide enough structural support for high-performance or heavy-duty drones.
For examples of these acronyms visit our Industries page.
As the CEO of Flyeye.io, Jacob Stoner spearheads the company's operations with his extensive expertise in the drone industry. He is a licensed commercial drone operator in Canada, where he frequently conducts drone inspections. Jacob is a highly respected figure within his local drone community, where he indulges his passion for videography during his leisure time. Above all, Jacob's keen interest lies in the potential societal impact of drone technology advancements.